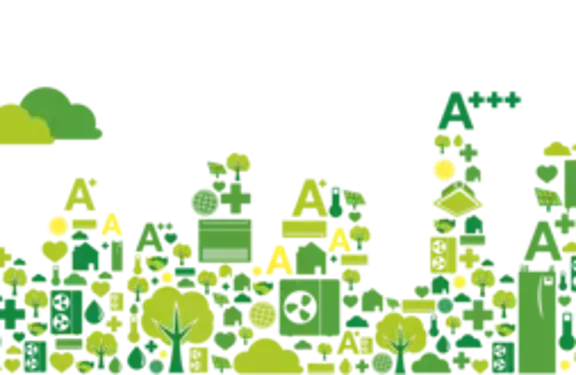
The Ecodesign Directive (ErP Directive)
My Ecodesign
My EcodesignOur use of energy is changing – not least from the perspective of European legislation. The ErP Directive, also known as the Ecodesign Directive, ensures that ‘Energy-related Products’ have to be clearly labelled. This page explains the key content of the ErP Directive in relation to air conditioning technology and heat pumps.
Regardless of whether you wish to efficiently heat or cool, we can help you find the right solution that meets your needs while also protecting the environment. Shape the future with us!
We have made available all the technical data sheets on our air conditioning and heat pump systems.
Facts and figures
Facts and figuresThe Ecodesign Directive / ErP (Energy-related Products)
ErP DirectiveThe European Green Deal
The European Union has set high climate protection targets to be achieved by 2050. These are collectively defined in the European Green Deal. The aim is for the European Union to reduce its greenhouse gases to zero by that point and thereby become the first climate-neutral continent.
These goals are to be implemented using a variety of means including the Ecodesign Directive (Energy-related Products, ErP), which defines the handling of energy-consuming products in 31 lots. The ErP Directive is intended to support resource conservation and energy efficiency in product design through the use of suitable political instruments.
Its effects therefore extend to PCs, dryers, vacuum cleaners, boilers and windows, to name just a few examples. A framework directive defines which product groups are affected and which framework conditions apply. Energy-consuming products are affected if they fulfil the following criteria:
- Minimum annual sales in the EU of 200,000 products
- Significant environmental impact of product
- Significant potential for improving environmental tolerability at reasonable cost
The goal of the Ecodesign Directive is to reduce indirect greenhouse gas emissions caused by the generation of energy. Direct greenhouse gas emissions from heat pumps or chillers, which may be caused by escaping refrigerant for example, are regulated by the F-gas Regulation (517/2014). This means that lawmakers seek to reduce indirect greenhouse gas emissions in two distinct ways.
As a manufacturer, we are legally obligated to only sell units that meet the requirements of the ErP Directive – even if the design and conception of the unit took place prior to this date. Mitsubishi Electric ensures that all its available units strictly adhere to the efficiency criteria of the Ecodesign Directive and are also approved for the purpose in question.
The provisions of the Ecodesign Directive
The Ecodesign Directive is based on two implementing regulations:
1. Ecodesign Regulation for CE labelling
2. Energy Labelling Regulation
Labels in the Ecodesign Directive
LabelsCE labelling
The Ecodesign Directive defines minimum efficiency and minimum emission standards. Products that do not meet these standards are not awarded the CE marking and may no longer be imported into the EU. This encourages manufacturers in particular to work with technologies that are CE-compliant, now and in the future.
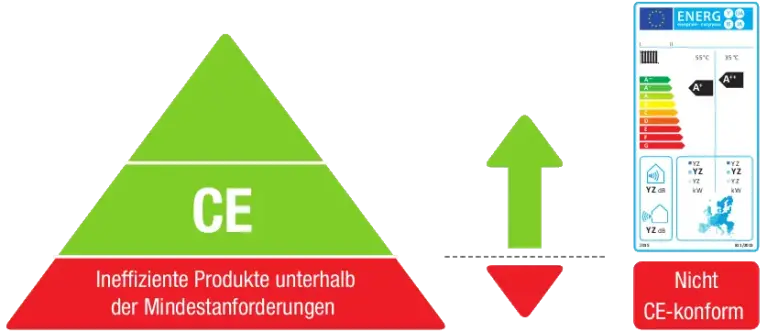
The energy label
The Energy Labelling Regulation sets out how the energy labels should look. It defines which values are needed for classification within a specific efficiency grade. Above all, the labels are intended to help consumers compare products and select them based on their efficiency. Units that feature a higher capacity for use in the commercial sector do not need to be identified with a label.
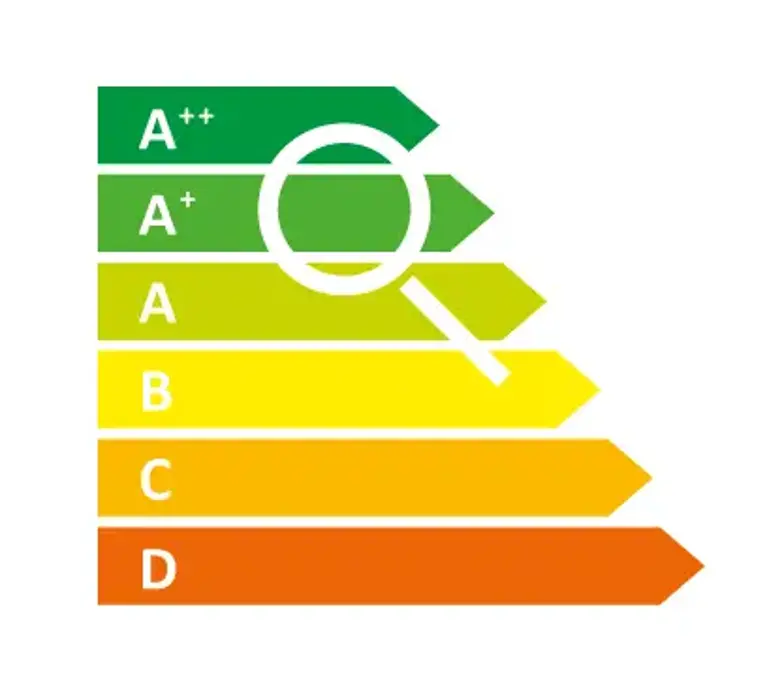
Seasonal measurement criteria for cooling and heating modes prior to the ErP Directive
Prior to the ErP DirectivePrior to the ErP Directive: performance measurement at only one measuring point in cooling and heating mode
Prior to 2013, air conditioning units were only rated by their EER and COP – and heat pumps only by their COP. EER rated efficiency in cooling mode, while COP defined efficiency in heating mode. The values were geared towards a single operating point, providing a less realistic picture that was to the disadvantage of consumers. The performance data is only recorded at a single measuring point during full-load operation for COP and EER.
Seasonal measurement criteria for cooling and heating modes with the ErP Directive
With the ErP DirectiveImplementation of the ErP Directive: optimised performance measurement at four measuring points in cooling and heating mode
The performance data for SEER and/or SCOP is recorded at four different measuring points in line with DIN EN 14825. The measuring points are weighted differently according to the temperature curves of the reference climate in Strasbourg, in order to reflect the energy efficiency of the unit under the most realistic conditions possible.
The following are also taken into consideration:
- Thermostat Off consumption
- Standby consumption
- Crankcase heater
The recorded SCOP value is included in the calculation of the seasonal space heating energy efficiency (ηs) within Lot 1. Space heaters have to meet certain minimum requirements depending on the energy carrier used. The yardstick for heat pumps is significantly higher than for all other technologies. The energy efficiency of hot water heating (ηwh) is relevant for the energy efficiency classification in Lot 2.
For Lot 6 and Lot 21 (room air conditioning units and air-to-air heat pumps over 12 kW), the SEER and SCOP values are applied when calculating the annual performance ratios ηsc and ηsh.
The ErP documentation
ErP documentationAll ErP data sheets ready to download
Manufacturers are required to provide corresponding ErP data sheets for all products on a public website. The information featured on the data sheets varies depending on the lot in question.
We have made available all the technical data sheets on our air conditioning and heat pump systems.
Find out more about the Ecodesign Directive for Mitsubishi Electric products
Technology for the long termOur technology – long-term solutions
We are constantly evolving our product range in line with our slogan ‘Changes for the Better’. All our systems are designed for energy-saving and whisper-quiet operation. Lorem ipsum
Ecodesign Directive for air conditioning units
Ecodesign Directive for heat pumps
FAQ – the ErP Directive
DirectiveIn accordance with the new Directive, manufacturers of chillers must align their products with the new Ecodesign requirements as of 1 January 2018. To the extent that limit values for energy efficiency are defined in an implementation measure, manufacturers are not allowed to bring products onto the market that fail to comply with these limit values (by undershooting them). In future, all products that do not fulfil these requirements must be adapted by the manufacturers or removed from the range.
The Ecodesign Directive (2009/125/EC) is a framework directive that does not in itself define any detailed requirements for specific product groups. Different products are divided up into so-called lots. The defined requirements must be observed and documented in production. The implementation measures applied to chillers are divided into different lots depending on the application and system design in question. The key product groups with regard to chillers are LOT 1 ENER, LOT 21 ENER and LOT 1 ENTR.
In contrast to other product groups, the requirements for chillers have been agreed with extremely tight deadlines for their implementation. The Regulation for LOT 21 ([EU] 2016/2281) was only published on 30 November 2016. With tier 1 entering into force on 1 January 2018, the market participants had only 13 months in which to adapt their range and planning documents to meet the new requirements. This was further complicated by the fact that the stipulated limit values were higher than had been expected. Tier 2 was subsequently introduced on 1 January 2021, featuring a further tightening of the limit values for the overall energy balance.
Depending on the design temperature and the performance capacity, the chillers may indeed belong to different lots or be required to comply with higher or lower energy efficiency limit values. This is because different energy efficiency limit values apply in terms of evaluation as a comfort chiller for room air conditioning, as a process chiller with a high operating temperature and as a process chiller with a medium operating temperature. It must be noted that chillers with a capacity of less than 400 kW and which can only perform cooling belong to Lot 21. Heat pumps that are used for cooling and heating and provide less than 400 kW belong to Lot 1, since they count as heat pumps.
Chillers for comfort air conditioning with more than 400 kW and up to 2 MW belong to Lot 21. In the case of a series of units that are used for cooling and heating and feature a capacity range of e.g. 300 kW to 900 kW, the initial units will belong to Lot 1 and the remainder will belong to Lot 21. In Lot 21, chillers for comfort air conditioning up to 2 MW are further subdivided for evaluation by their system and capacity level. Air-cooled comfort chillers are divided into capacity levels above and below 400 kW and must meet different requirements as a result.
In terms of water-cooled units, lawmakers distinguish between units with less than 400 kW, between 400 kW and 1,500 kW, and more than 1,500 kW of cooling capacity. When it comes to the minimum energy efficiency of process chillers, a distinction is made on the basis of the operating temperature. Process chillers with a high operating temperature (cold water outlet from +2 °C to +12 °C) and up to 2 MW belong to Lot 21. In contrast, process chillers with a medium operating temperature (media outlet temperature down to 8 °C) and low operating temperature (media outlet temperature down to -25 °C) must be evaluated using the implementation regulation ENTR LOT 1 (2015/1095). It is also worth mentioning that units above 2 MW and those with a split design (chillers and external liquefier) are not currently governed by any Ecodesign Directive.
Specialist planners and installers are generally obligated to implement the part of the system for which they are responsible in accordance with the specific and technical rules of their trade. However, responsibility for the implementation of and adherence to the Ecodesign Directive is the responsibility of the system distributor and not its creator. The decisive date is that on which the units were dispatched from a factory within the EU. This means that, as of 1 January 2018, units may no longer be dispatched from factories if they do not meet the requirements – even if the planning and design stages were completed beforehand.
In addition, specialist planners and system constructors must have the manufacturer confirm the ErP conformity of the ηsc efficiency level for the comfort chiller and the SEPR value for process chillers. This self-declaration is performed by the manufacturer or importer by attaching the CE label and issuing a declaration of conformity. In addition to the CE declaration, the manufacturer must enclose a product data sheet known as the product fitch. Within a defined template, manufacturers must state further technical parameters in addition to the SEER or SEPR values. This makes it possible to ensure that the calculations in the respective tiers can in fact be achieved and that the products comply with the ErP Directive upon dispatch.
The decisive date in this regard is that of dispatch from the factory, not that of commissioning. The creator or operator of the system should nevertheless ensure that the product is installed and used according to the declaration. Although a process chiller can also be used for comfort air conditioning, only the manufacturer can check and certify whether this unit additionally meets the annual performance ratio requirements in relation to room cooling.
In order to achieve the necessary chiller efficiency for room air conditioning or process cooling, manufacturers are responding to the new Ecodesign Directive with numerous innovations. These include the use of inverter technology in scroll, screw and magnet bearing turbo compressors. Efficiency can be considerably increased through the use of variable-speed pumps and EC fans. Optimised control technology with load- and temperature-dependent setpoint adjustment contributes to increased seasonal energy efficiency. Evaporators flooded with refrigerant also offer a constructive and efficient solution.
The timetable for the potential development stages is depicted in an overview diagram featuring a pair of examples of comfort air conditioning – one each for air-cooled and water-cooled chillers respectively. The information presented here provides a means of achieving the stipulated efficiency values. Based on the cooling capacity and SEER values, it is possible to identify the technical innovations for the individual units according to tier 1 (as of 2018) and tier 2 (as of 2021).
Among air-cooled units (diagram 1) with a capacity below 30 kW, the trend since January 2018 has been in favour of installing inverter-controlled compressors. In the case of units with a capacity of 30 kW to 400 kW, uncontrolled scroll compressors can continue to be used. Units that feature screw compressors and have more than 400 kW of cooling capacity controlled via an output regulator may also fulfil the new requirements.
In the second tier as of 2021, the equipment required at the respective capacity levels must be increased once again in order to achieve the necessary minimum energy efficiency. Variable-speed screw compressors are therefore being deployed more frequently at capacity levels above 400 kW. Water-cooled units (diagram 2) follow a similar timetable.